Introducing the Liebherr LR 1300.2 SX Unplugged: Experience the electrifying power of innovation.
- cranehub
- Feb 19
- 3 min read
The Liebherr LR 1300 crawler crane proudly marks its 18th anniversary this year. At the 2025 Bauma exhibition, Liebherr is unveiling the 300-tonne model in its first-ever battery-powered, unplugged version, offering the significant advantage of zero emissions. The inclusion of a derrick counterweight greatly expands the range of applications for this innovative crane system. A comprehensive suite of digital assistance systems and ground pressure reduction plates are implemented to ensure the utmost safety during operations.

Munich (Germany), 18 February 2025 – The LR 1300.2 SX unplugged operates with a 438 kW electric motor and can function unplugged for up to 13 hours, depending on the application, thanks to its 392 kWh battery. The duration of a complete battery-charging process varies between 4.5 to 8.5 hours, depending on the available infrastructure at the job site, allowing normal operations to continue during charging. Whether connected to an electric supply or operating unplugged, the performance and versatility remain consistent. A standout feature of the unplugged version is its zero-emission operation, producing no exhaust fumes and maintaining a remarkably low noise level, making it particularly suitable for noise-sensitive or urban environments, benefiting both job site personnel and nearby residents.

For demanding lifting tasks and extended boom configurations, the lifting capacities of the LR 1300.2 SX unplugged can be enhanced through the use of derrick equipment. Fine adjustments to the suspended counterweight can be made without the need for an auxiliary crane. This new crawler crane can be outfitted with seven distinct boom configurations, reaching a maximum boom length of 169 metres. At Bauma, the LR 1300.2 SX unplugged will be showcased with a 20-metre main boom and an adjustable 20-metre jib. The Crane Planner 2.0 lift planning software allows for precise determination and simulation of the optimal boom combination tailored to specific construction site requirements in advance.
Liebherr has designed a specialized operating mode for lifting operations on floating units. This mode incorporates load curves for various inclinations (0°, 1°, 2°, 3°) with appropriate load moment limitations for enhanced safety. The inclination of the floating unit is continuously monitored and displayed to the crane operator, with warning alerts issued if permissible limits are exceeded. The load curves are adjusted according to the detected inclination, and measures are in place to prevent exceeding the maximum boom angle during load placement. A proven assistance system, the vertical line finder, is integrated into this new safety concept, enabling the crane operator to eliminate diagonal pulls at the touch of a button, particularly those arising from shifts in the center of gravity during load handling.
During the crane's design process, Liebherr prioritized safety. A notable feature is the gradient travel aid, which ensures secure navigation across slopes. The crane's control system automatically calculates the center of gravity and alerts the operator before the crane exits the safe operating area. While in motion, the operator is provided with real-time data regarding permissible and actual gradients, as well as the crane's overall center of gravity. If necessary, adjustments to the main boom angle can be made to maintain safe operation.
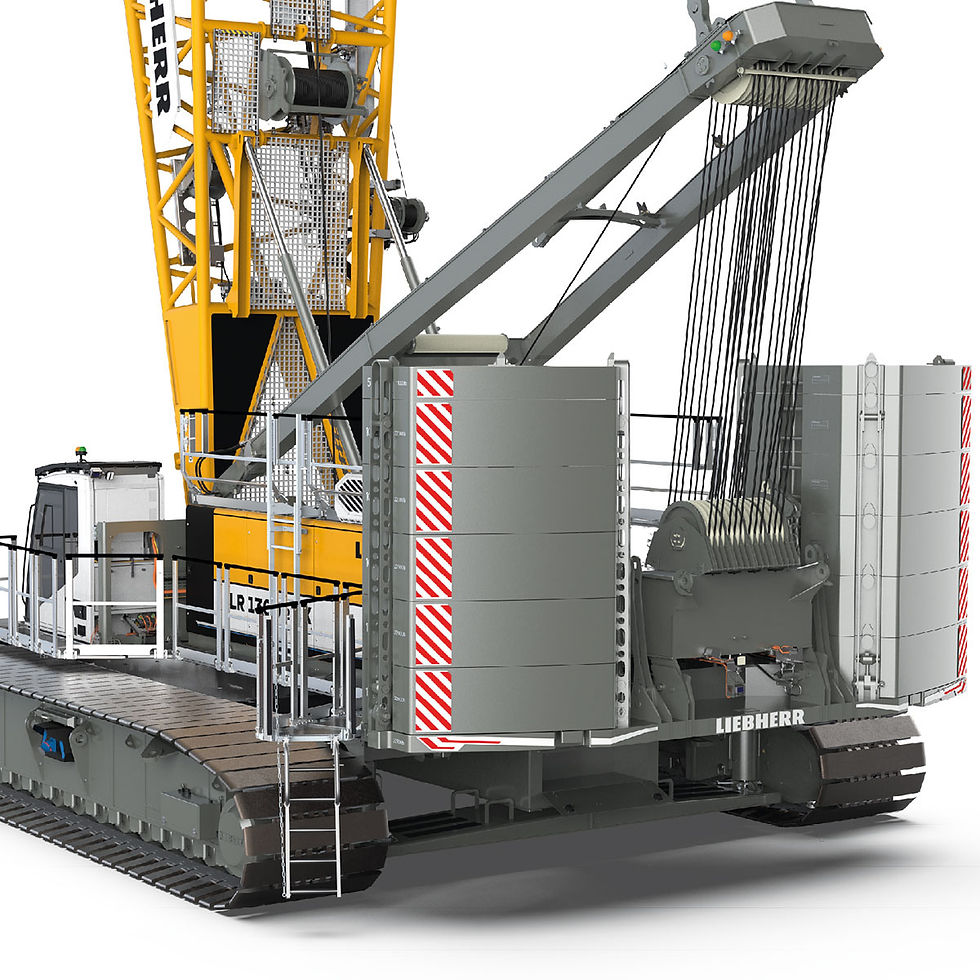
The crawler crane is equipped with a ground pressure display that continuously shows real-time ground pressure calculations. This feature keeps the operator informed about whether the crane is in or nearing a critical area. The LR 1300.2 SX unplugged can reduce its ground pressure by up to 56% using additional ground pressure reduction plates mounted on the front and rear of the crane. During lifting operations, these plates can be lowered to significantly enhance the crane's ground contact area, providing an added safety measure when lifting long booms from the ground.
Additionally, the boom up-and-down assistant is an integral part of the safety concept. This assistance system alerts the operator as they approach the tipping threshold during boom erection or lowering and automatically halts operations before entering an unsafe zone. The operator is no longer required to manipulate the winches of the main boom and jib separately; instead, controlled folding of the jib can be initiated with the press of a button. The speed of the lowering procedure is managed through a single joystick, with the boom up-and-down assistant determining the safest method for lowering the boom.
Comments