Crane Hub Lift of the Month February 2025 - Successful and Efficient Load-Out of the First Wind-Powered Offshore Gas Platform in the Dutch North Sea by Mammoet
- cranehub
- Mar 5
- 3 min read
Expertise in heavy lifting significantly accelerates project timelines while enhancing contingency planning.

The N05-A platform marks a milestone as the first offshore gas platform in the Dutch North Sea to operate entirely on wind power, utilizing electricity sourced via cable from the adjacent 113.4 MW Riffgat offshore wind farm.

This platform is an integral component of the GEMS (‘Gateway to the Ems’) project, which is dedicated to the development of field N05-A and surrounding fields located in the waters along the Netherlands-Germany border. The electrification of the N05-A platform is projected to lead to a remarkable reduction in carbon emissions, exceeding 85% throughout the project's lifecycle.

Mammoet was engaged by HSM Offshore to facilitate the load-out of the 3,050-ton N05-A topside and the 3,150-ton jacket at HSM’s fabrication facility located in Schiedam, Rotterdam.
Mammoet’s responsibility for the project entailed the successful load-out of both components onto a barge for maritime transport. The offshore sailing and installation processes were managed by ONE-Dyas, the platform's owner.

Through a strategic engineering approach, Mammoet enabled the jacket to be assembled more efficiently in proximity to its installation site, thereby reducing construction lead time.
The assembly and weighing of the jacket and topside were executed using mobile cranes, conventional trailers, and Self-Propelled Modular Transporters (SPMTs).

The initial operational phase of the project involved assisting with the movement and assembly of the jacket, which was fabricated and constructed in two segments.
Mammoet facilitated the heavy transport and upending of the jacket’s sections employing four mobile cranes: two LTM 1650 (650-ton) cranes and two LTM 1450 (450-ton) cranes. The installation of the pile sleeves was accomplished with the aid of a 750-ton mobile crane.
Upon reaching the correct positioning, the top section of the jacket was relocated to the quayside, where heavy lifting operations were conducted using two sheerlegs. This maneuver created the necessary space for the bottom section to be positioned underneath for a seamless connection.
Self-Propelled Modular Transporters (SPMTs) were utilized to maneuver the topside outside the fabrication facility and onto the quay. Mammoet subsequently assisted in the installation of a pedestal crane onto the topside using conventional trailers and mobile cranes.
With the jacket and topside fully assembled, both components were lifted by SPMTs, and their final weights were accurately determined using Mammoet load cells. The load-out operation commenced following the weighing of both structures.
Shipping both parts of the offshore gas platform concurrently was essential to adhere to the project schedule.
One of the primary challenges faced during this project was the load-out phase. Typically, a barge would accommodate either a topside or a jacket for loadouts of this nature; however, in this instance, both structures had to be loaded onto the same vessel to expedite the overall timeline.
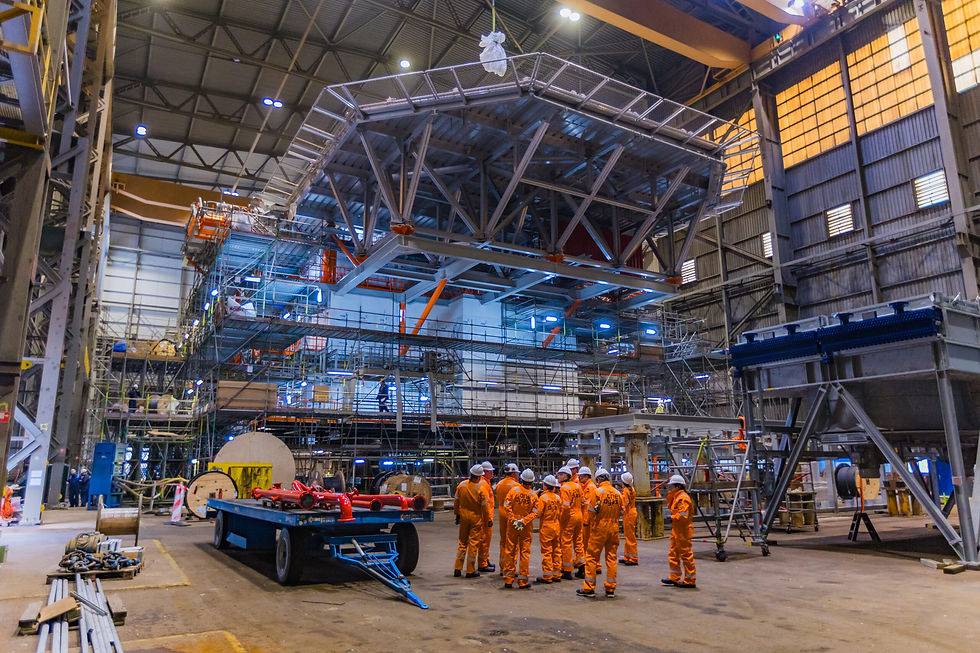
This requirement posed spatial and engineering challenges, necessitating accommodations for the installation of pumps and winches on the transport vessel. The combined loads also prohibited the application of conventional mooring techniques.
“The mooring was particularly critical, necessitating extensive engineering,” explains Sven Segeren, Project Manager at Mammoet. “Ordinarily, we would implement a winch configuration to moor and stabilize the vessel, yet this was not feasible due to the substantial forces exerted by the heavy loads.
The winch loads exceeded safe limits, and the bollards lacked sufficient strength; thus, we employed a small spud leg barge to secure the vessel and maintain its position throughout the load-out process.”

Preparation of the main barge took five days, during which ballast equipment was installed, pre-ballasting was performed, and sailing conditions were assessed for the final location.
The load-out operation for both the jacket foundation and topside was successfully completed in just two days, utilizing four trains of 32 axle line SPMT trailers for transport.
Due to external factors beyond the project's control, the execution date remained uncertain for an extended period. Consequently, Mammoet was tasked with preparing a temporary load-in venue to ensure the continuity of subsequent projects at the HSM Offshore yard.
The team organized Mammoet’s own yard in Schiedam, adjacent to HSM Offshore, to facilitate the load-in of the topside and jacket. This involved preparing an area for temporary storage of the components, reserving necessary equipment, and creating essential engineering plans.
Ultimately, this designated space was not required; however, Mammoet demonstrated agility and adaptability in response to a dynamic operational environment.
“We maintain a strong collaborative relationship with HSM Offshore, engaging with them at the outset of projects to provide innovative assembly solutions,” adds Segeren.
“Through effective collaboration and our early involvement, we successfully devised a strategic approach for the assembly of the jacket, thereby minimizing construction lead time.”
Comments